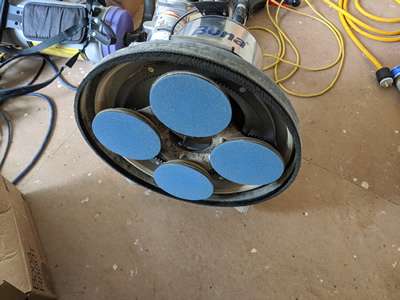
by Everett 4/18/2020
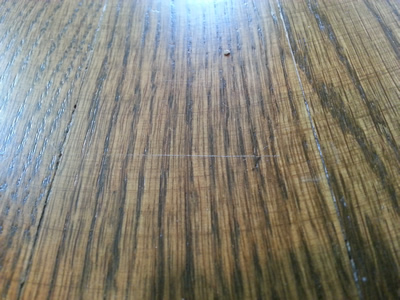
When I look back on my 20 plus year career in wood flooring, there are countless instances of things we did that were outright unthinkable these days but went unnoticed for years. Whether it’s the quality of the sand job, staining, finishing, etc., it’s a wonder to me that we thought we were doing such high end work considering how far we’ve come. I look at it as a long line of small advancements, this post will cover the series of improvements we’ve come up with in the quest for the swirl-less stain job. Back in the late 90s when I first started doing this, the guy I worked for would final sand using 100g resinite paper bolted onto a hard plate on a buffer. We rarely stained jobs back then, because he didn’t use screens. Just imagine how bad the swirls were on those floors when stained. And random orbit sanding the edger marks out? That wasn’t even on the radar (that’s also an important aspect of a quality stain job but won’t be the focus of this post). We even abraded between coats with used 100g paper on the buffer if you can even imagine such a thing. Soon after we started out on our own, we discovered sanding screens. It's crazy to think about someone not even knowing about screens in retrospect, but either way it was a huge step forward for us.
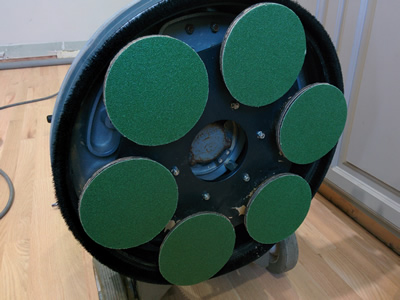
But eventually we started to notice that we were in fact still leaving some pretty bad swirls in our stain jobs, nothing like a hard plate, but they were there nonetheless. I know some guys still cling to the “old school” ways of sanding floors and stand by standard sanding screens under standard buffers, “clocking” and all that, but you can’t clock a buffer in every situation and I’ve never had much luck with it. Eventually we decided to try out the Bona MultiDisc multi head buffer attachment. It’s just a buffer block with 6 freewheeling heads 5” in diameter. This was yet another small advancement for us, depending on the stain color it would produce some very nice floors with barely noticeable swirls. And the swirls it did leave were smaller and shaped differently than a big sweeping swirl from a 17” sanding screen.
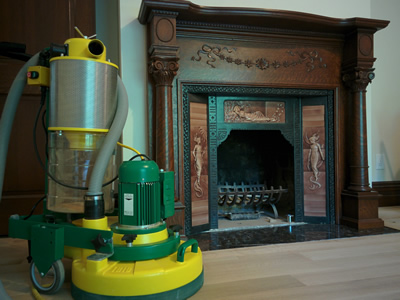
This “worked” for years but eventually much like before, you start to notice more and more that it’s just not perfect, and we started searching again for the mythical swirl free stain job. Up next was not just an attachment for a buffer, but a whole new pricey machine- the Lagler Trio. This machine has 3 driven sanding heads 8” in diameter that each spin while the whole thing spins. We didn’t buy this machine just to final sand for stain jobs, it’s one of the best sanding machines on the market for sanding a floor perfectly flat, but that’s another story. It also does an amazing job when used with sanding screens under it- especially Norton Red Heat screens. From what I understand, most of the time when you get a bad swirl, it’s caused by a rogue piece of grit that breaks off and rolls around under the sander until it flings out the side and gets sucked up by the dust collection. One of the huge benefits of Red Heat is that it has excellent grit retention- meaning the sanding media sticks to the paper or screen really well and doesn’t break off as much. If we had used Red Heat screens under our standard buffer I might not have had much content for this post, but we didn’t know any of this back then.
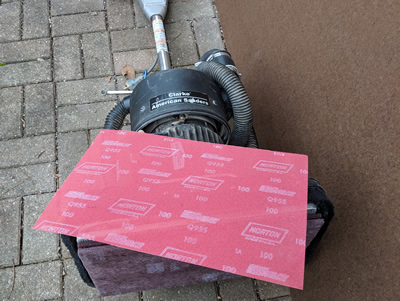
Anyway, the Trio did and still does an excellent job, much better than the multidisc and the paper we were using with it. But every once in a while there would be a swirl here and there that would get missed, it’s very difficult to set up, and with no light it’s hard to tell if you’ve gotten all the scratches from the previous grit cut out. Again, a step forward but still not perfect. So once again the search for the next machine or abrasive began. I kept hearing intriguing things from Wayne Lee and others about the American Sanders OBS-18, or “Squarebuff” 12”x18” sander that you can rent from Home Depot of all places. Really it’s just a gigantic palm sander, but apparently is capable of producing the storied swirl free stain job. After a few months of calling the Home Depot used equipment sales department, they finally had one available and we picked it up. Because I was already familiar with the effectiveness of Red Heat screens under the Trio, I had to see if they made them for the OBS-18 and luckily they did. This finally led to the perfect swirl free stain job. When you absolutely need to pull off the perfect job, the OBS-18 combined with Norton Red Heat screens is certainly up to the challenge.
The only problem with the OBS-18 is that it doesn’t have a light and I have no frame of reference for when a screen is too dull. You don’t get the same kind of feedback from the OBS-18 that you do from a buffer. I find myself stopping constantly to check the floor up close with a worklight. It works, and works well, but there’s still the possibility of missing a scratch from a previous machine/grit. I should also note that I have to take the previous machine up to the same grit that I plan on using with the OBS-18, I can’t for instance sand up to 80g with a planetary sander then skip to 100g on the OBS-18, it has to be taken up to 100g before the OBS-18 comes out in my experience.
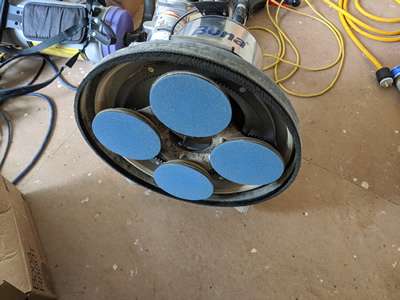
We’re so close. It’s “perfect”, but it’s not perfect. We’re still on the hunt for the reliably swirl free stain job, but where can we possibly go from here? It seems like we’ve tried everything. Enter Norton’s new MeshPower hook and loop screens. Normal sanding screens are double sided and need to be driven with something like a maroon pad under the weight of a machine. Hook and loop screens are basically screens with grit on one side, velcro on the other so they can be used on machines that use hook and loop abrasives. We’ve used Mirka’s Abranet screens for random orbit sanding out edger marks for years so right away I knew that MeshPower would take over in that regard. What I hadn’t considered was using them on the field under the Bona PowerDrive (another planetary sander on the market, it uses 4 driven heads 6” in diameter) or MultiDisc. I kept seeing testimonials from guys producing near perfect floors with these, and not only that but getting upwards of 1200 square feet out of one set(!)
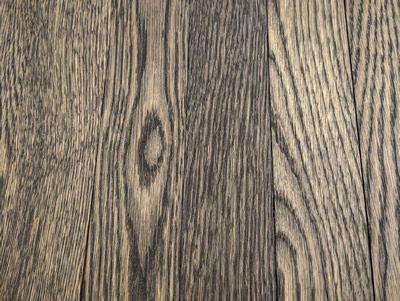
We were doing a job that was to be water popped (water popping allows you to “get away” with a little more when it comes to swirls) and I decided to try it out. To really push the envelope I planetary sanded up to 80g then skipped to 100g MeshPower. With the light on the PowerDrive I could clearly see the 80g scratches getting cut out with each back and forth pass I made, and I felt like I was walking at a pretty fast pace too. This job was 900 square feet so given the life other guys are getting out of these, I didn’t see any reason to change these at all and sure enough they lasted the whole time. I wasn’t walking at a snail’s pace towards the end either. Usually you can tell if a sand job is going to look bad before the stain goes on if there’s some kind of problem, but I didn’t want to get too overconfident too soon. Maybe I should have- this stain job was PERFECT.
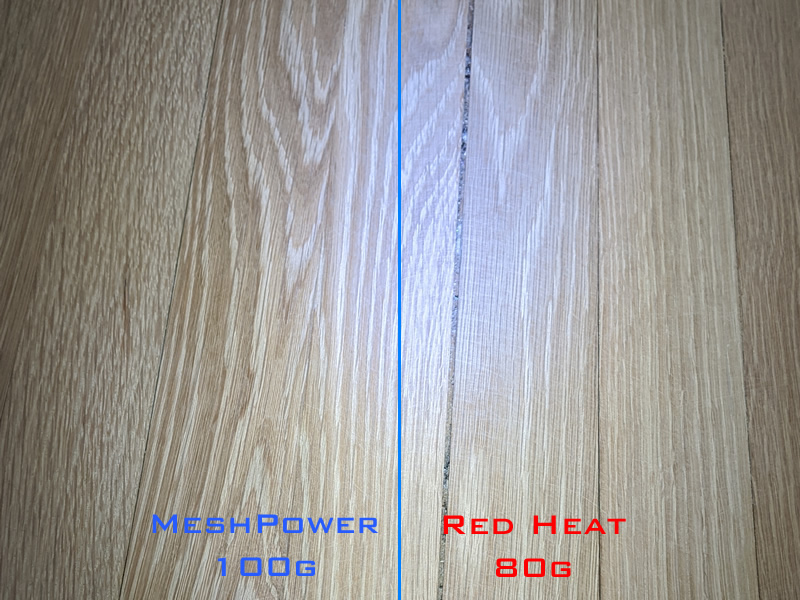
I’m sold, this is now my go-to procedure for stain jobs. It’s reliable, saves time and money, and I can finally stop worrying about that looming stain day. Many thanks to Nathan Kelly, hiring that guy was the best move Norton ever made.